US READY - The American's No1 Manufacturer of Agricultural Machinery
The Advantages of Mechanical Power & Machinery in Agriculture
The Advantages of Mechanical Power & Machinery in Agriculture
Combines and mechanized irrigation systems may not seem all that radical these days, but they weren't always around: the widespread availability of agricultural products in developed countries is a testament to the mechanical advances that have propelled agriculture into the 21st century, and freed up people's lives beyond the farm.
Ag Mechanization Over Time
As Purdue University notes, devices used in plowing and cultivation have been used in agriculture from earliest times. While these earlier animal-propelled implements improved over the centuries, it was not until the introduction of the cotton gin, patented in 1794, and the mechanized reaper in the 19th century that the industrialization of agriculture took off in earnest. The 20th century saw the disadvantages of the previous century's steam-powered tractors and threshers overcome with the debut of the gasoline engine, precipitating the development of gas-powered farm tractors and effectively marking the transition from horse- to machine-powered agriculture.
Efficiency Improvements and Problem-Solving
Increased use of tractors in American agriculture, from the hundreds used in the early 1900s to over 3 million in 1950, allowed farming to be conducted on an unprecedentedly large and increasingly efficient scale. Technical innovations in the tractor introduced automated cultivation and planting via the tricycle-style tractor, while rubber tires sped up production and treads subverted the problem of tires sticking in soft soil. Use of four-wheel drive and diesel power, along with electronically controlled tractor systems, brought new levels of tractor pulling power to the farming landscape, while driving down the need for human labor.
Labor Reduction and Cost Savings
According to the National Academies, the advent of Agricultural Machinery throughout the 20th century contributed to a 75 percent reduction in labor required to produce and harvest hay, corn and cereal grains. Specific developments, such as self-tying hay and straw balers, and spindle cotton picker of the 1940s, as well as the rotary and tine separator combines of the 1970s, were instrumental in reducing labor. Despite the variations in crop type and harvesting methodology, farming magazine Choices notes that mechanical harvesting can cut costs in cases where some damage to the fruit or vegetable is permitted.
Crop-specific Advancements
Additional advantages of mechanization for certain delicate crops that traditionally rely on on hand-picking are that machines eliminate some of the disadvantages of human handling. As Choices notes, for example, the BEI Black Ice Harvester is a machine that creates a localized turbulent environment, loosening ripe berries from the bushes. The mechanized agitation does not require any human hands to touch the fruit, thus reducing food safety concerns, and the absence of any rotating mechanisms allows multiple passes on the same plant with minimal damage to the berries and bushes.
Farm Machinery Selection
Use this decision tool to estimate the number of field days required to complete a field operation.
Farm Machinery Selection
Putting together an ideal machinery system is not easy. Equipment that works best one year may not work well the next because of changes in weather conditions or crop production practices. Improvements in design may make older equipment obsolete. And, the number of acres being farmed or the amount of labor available may change.
Because many of these variables are unpredictable, the goal of the good machinery manager should be to have a system that is flexible enough to adapt to a range of weather and crop conditions while minimizing long-run costs and production risks. To meet these goals several fundamental questions must be answered.
Machine Performance
First, each piece of machinery must perform reliably under a variety of field conditions or it is a poor investment regardless of its cost.
Tillage implements should prepare a satisfactory seedbed while conserving moisture, destroying early weed growth and minimizing erosion potential. Planters and seeders should provide consistent seed placement and population as well as properly apply pesticides and fertilizers. Harvesting equipment must harvest clean, undamaged grain while minimizing field losses.
The performance of a machine often depends on the skill of the operator, or on weather and soil conditions. Nevertheless, differences among machines can be evaluated through field trials, research reports and personal experience.
- Machinery Costs
Once a particular type of tillage, planting, weed control, or harvesting machine has been selected, the question of how to minimize machinery costs must be answered. Machinery that is too large for a particular farming situation will cause machinery ownership costs to be unnecessarily high over the long run; machinery that is too small may result in lower crop yields or reduced quality.
- Ownership Costs
Machinery ownership costs include charges for depreciation, interest on investment, property taxes, insurance and machinery housing. These costs increase in direct proportion to machinery investment and size.
- Operating Costs
Operating costs include fuel, lubricants and repairs. Operating costs per acre change very little as machinery size is increased or decreased. Using larger machinery consumes more fuel and lubricants per hour, but this is essentially offset by the fact that more acres are covered per hour. Much the same is true of repair costs. Thus, operating costs are of minor importance when deciding what size machinery is best suited to a certain farming operation.
A detailed procedure for estimating machinery ownership and operating costs can be found in AgDM Information File A3-29 Estimating Farm Machinery Costs (PM 710).
- Labor Cost
As machinery capacity increases, the number of hours required to complete field operations over a given area naturally declines. Estimates of time requirements for completing machinery operations are found in AgDM Information File A3-24 Estimating the Field Capacity of Farm Machines (PM 696).
If hourly or part-time hired labor operates machinery, it is appropriate to use the wage rate paid, plus the cost of any other benefits which may be provided, as the labor cost. If the farmer-owner or a hired worker who is paid a fixed wage operates machinery, then it is proper to value labor at its opportunity cost, or the estimated return it could earn if it were used elsewhere in the farm business, such as in livestock enterprises.
In many cases, crop yields and quality are affected by the dates of planting and harvesting. This represents a “hidden” cost associated with farm machinery, but an important one nevertheless. The value of these yield losses is commonly referred to as “timeliness costs.”
- Total Machinery Costs
Figure 1 illustrates the effect that changes in machinery size have on each type of cost in a typical situation. For very small machinery (relative to crop acres), a slight increase in machinery size can lower timeliness and labor costs significantly, enough to more than offset the higher fixed costs. However, as machinery size continues to increase, the timeliness cost savings diminish, and eventually total costs begin to rise. One objective of machinery selection, then, is to select machinery in the size range where total machinery costs are lowest.
Factors That Affect the Size of Machinery Needed
Machinery recommendations must be based on the characteristics of each individual farm. The following factors influence machinery selection, and are discussed in order of importance.
- Number of Crop Acres
As more crop acres are farmed, larger-scale machinery is needed to ensure that planting and harvesting are completed in a timely fashion. An alternative is to acquire a second unit of some machines, if an additional tractor and operator are available.
- Labor Supply
The number of acres that can be completed each day is the most critical measure of machinery capacity, more than machine width or acres completed per hour. Increasing the labor supply by hiring extra operators or by working longer hours during critical periods may be a relatively inexpensive way of stretching machinery capacity. In addition, the cost of additional labor only needs to be incurred in those years in which it is actually used, while the cost of investing in larger machinery becomes “locked in” as soon as the investment is made. On the other hand, extra labor may not always be available when needed, and working long hours over several days can present a safety hazard.
- Tillage Practices
The number of field days needed before planting is completed depends partly on the number of separate operations completed on each acre. Reducing the number of tillage practices performed or performing more than one practice in the same trip effectively decreases the amount of machinery capacity needed to complete field operations on time. Of course, machinery cost savings from reduced tillage must be compared to possible increased chemical costs and effects on yields.
- Crop Mix
Diversification of crops tends to spread out the periods when timely completion of field operations is critical. For example, yield reductions due to late planting begin later for soybeans than for corn. Harvesting can also be completed over a longer time period. Thus, growing more than one or two crops reduces the machinery capacity needed for a given number of crop acres. However, it may also require purchasing additional types of machinery, especially for harvesting.
- Weather
Weather patterns determine the number of days suitable for fieldwork in a given time period each year. Although actual weather conditions cannot be predicted far enough in advance to be used as an aid to machinery selection, past weather records can be used as a guide. AgDM Information File A3-25 Fieldwork Days in Iowa (PM 1874) lists the number of suitable field days expected for different periods of the year in each of the nine crop reporting districts in Iowa. As a rule of thumb, weather is suitable for field work about 60 percent of the time in the spring and about 75 percent of the time in the fall. This does not take into account time off for holidays, Sundays or other occasions. Machinery selection should be based on long-run weather patterns even though it results in excess machinery capacity in some years and insufficient capacity in other years.
- Risk Management
Fluctuations in the number and occurrence of suitable field days from year to year cause timeliness costs to vary even when the machinery set, number of crop acres and labor supply do not change. Investing in larger machinery can reduce the variability of net machinery costs by ensuring that crops are planted and harvested on time even in years in which there are few good working days. Machinery fixed costs would be higher with larger machinery, but they would not fluctuate as long as the machinery set did not change. Farmers with high fixed cash flow needs, such as land mortgage payments, may be willing to pay more (in higher fixed machinery costs) than other operators for the “insurance” of not suffering substantial yield losses due to late planting and harvesting in certain years.
Planting and Harvesting Dates
Long-term studies indicate that corn yields typically start to decline significantly when planting occurs after May 10 to 14. The exact dates will vary from year to year. About 50 percent of Iowa’s corn is normally planted by this time. One reason for the decline in yield for late-planted corn is that fewer “heat units” are available during the growing season, and this influences the rate of crop development.
How early to start planting requires considerable judgment. Ideal conditions would be a soil temperature of 50°F (10°C) or above at planting depth and a favorable five-day weather forecast. In most of Iowa, if soil conditions and temperatures are favorable, starting to plant the last ten days of April should be advantageous. In May, the major consideration should be the condition of the seedbed.
There is some risk with early planting. Replanting may occasionally be required, but the long-term benefits far outweigh this cost. An added benefit from early-planted corn is lower grain moisture levels at harvest and reduced drying costs.
Most of the same things can be said about planting soybean varieties. The ideal time for planting adapted soybean varieties is between May 1 and May 15. Yields can be expected to decline in most years if planting occurs after May 20.
How Large Should Machinery Be?
One way to measure the capacity of a set of machinery is by the number of work days required to complete field operations. This depends on the number of crop acres, machinery operations performed, size of the machinery in use, and availability of labor.
In research conducted recently at ISU, total machinery costs for Iowa grain farms, including the value of timeliness losses, were estimated for a number of different machinery combinations. The effects of variations in the number of crop acres and labor supply, were compared.
Under each set of circumstances the machinery set for which total costs were lowest, including yield losses due to poor timeliness, was identified. In some cases, several machinery sets gave nearly identical minimum costs. In approximately 80 percent of the cases tested, the least-cost machinery sets were able to complete all tillage and planting operations in about 20 to 25 field days. A good rule of thumb for farmers who wish to have sufficient machinery capacity to reduce risk, as well as maintain total costs at a low level, is to be able to complete tillage and planting in about 20 field days.
Where less than one full-time person is available to operate machinery, a goal of 25 to 30 days for completing planting and tillage will most often minimize costs. On the other hand, farms with 2 or 3 full-time machinery operators available could aim to complete this work in less than 20 days.
The machinery sets which minimized total machinery costs were most often able to complete harvesting of corn and soybeans in 25 to 30 field days. As with spring work, operators for whom risk reduction is important should use the lower end of this range as a goal, although yield losses from late harvesting are generally not as severe as from late planting.
A number of different machinery combinations may allow fieldwork to be completed in the same number of days. In putting together a machinery set, it is also important to correctly match machinery sizes and tractor power. Using tractors with horsepower in excess of that required for the implement being pulled results in excessive depreciation and interest costs, while using too little horsepower may cause faster engine wearout.
Some farms may not have enough crop acres to justify owning a full line of machinery, particularly for harvesting. Custom hiring or leasing certain machinery operations may lower total costs as well as provide more flexibility in the amount of machinery capacity. For a detailed discussion of custom hiring, leasing, and renting farm machinery see AgDM Information Files A3-33 Combine Ownership or Custom Hire (PM 786) and A3-21 Acquiring Farm Machinery Services (PM 787).
Field Capacity
To project the number of field days required, it is necessary to know the field capacity for each implement.
Field capacity usually is measured in acres accomplished per hour, and is affected by three variables: width, speed and field efficiency.
Width refers to the effective working width of the implement, excluding overlapping, and is measured in feet. Speed, which is measured in miles per hour, refers to a safe operating speed under normal working conditions. This does not take into account slowing down to turn at the end of a field.
Field efficiency is the actual field capacity that can be achieved as a percentage of the maximum theoretical capacity without overlapping, slowing for turning or stopping to adjust machinery, fill containers, empty hoppers, and make minor repairs.
>> See More: US ready
How to use Farm Machinery
How to use Farm Machinery
Operating a Tractor
Tractors are the main cause of accidental deaths on farms. Over the years, many farmers, farm workers and others living on or visiting farms, have been killed or seriously injured falling from moving tractors, being run over by tractors, or being crushed when a tractor rolls sideways or backwards.
Spot the hazard
Regularly check for hazards relating to tractors, attached implements and field conditions. Hazard areas could include mechanical parts, operator training, other people, work procedures, unsafe jacking, climatic conditions, chemicals used, uneven terrain, and any other potential causes of an injury or a hazardous incident. Keep a record to ensure identified hazards are assessed and controlled.
Assess the risk
Once a potential hazard has been identified, assess the likelihood of an injury or hazardous incident occurring. For example, risk to children playing near a tractor will vary, depending on what the tractor operator is doing, how close they are to the tractor and whether the operator knows they are there. Consider ways of minimizing risk.
Make the changes
- Read and follow safety procedures in the manufacturer's manual.
- Ensure an approved cab or rollover protective structure (ROPS) is fitted.
- Fit and use a seatbelt on tractors with ROPS.
If there is a risk from falling objects, fit a fall-on protective structure (FOPS).
To reduce risk of back strain, fit a seat with side restraints and a backrest.
- Wear hearing protection, and remember, not all tractor cabs are sound proof.
- Keep children away from tractors and machinery.
- Remove starter keys when tractors are not in use.
- Have an up-to-date maintenance schedule.
- Follow safe maintenance and jacking procedures. (See Tractor Maintenance.)
- Ensure the operator is properly trained for each type of tractor work.
- Always mount and dismount on a tractor's left side - to avoid controls.
- Adjust the seat so all controls are safely and comfortably reached.
- Keep all guards in place, including the power take-off (PTO).
- Operate the self-starter from the operator position only.
- Never carry passengers.
When operating a tractor
- Drive at speeds slow enough to retain control over unexpected events.
- Reduce speed before turning or applying brakes.
- Watch out for ditches, logs, rocks, depressions and embankments.
- On steep slopes, without a trailed implement, reverse up for greater safety.
- Engage the clutch gently at all times, especially when going uphill or towing.
- Use as wide a wheel track as possible on hillsides and sloping ground.
- Descend slopes cautiously in low gear, using the motor as a brake.
- Never mount or dismount from a moving tractor.
- Ensure the park brake is on and operating effectively before dismounting.
- Take short breaks regularly when working long hours.
When towing implements
- Fit attachments according to the manufacturer's instructions.
- Always attach implements to the draw bar or the mounting points provided by the manufacturer.
- Never alter, modify or raise the height of the draw bar unless provided for by the manufacturer.
- Regularly check safety pins on towed lift-wing implements, to ensure they are not worn.
- Ensure all guards on towed implements are in place before operating.
- Never hitch above the centerline of the rear axle, around the axle housing or to the top link pin.
- Never adjust or work on implements while they are in motion
- Never attach implements unless the PTO shaft is guarded.
- When parking, always lower the three-point linkage and towed implement.
To avoid strain injury
- Adjust the tractor seat for back support and comfort
- When buying a tractor, ensure seating is safe and comfortable.
- Check seat height, seat depth, backrest height and angle, fore and aft movement, seat tilt, firm padding, partial pivoting (if you have to spend long periods looking behind you), and vibration-absorbing suspension.
- Dismount every hour or so, and spend 5 or 10 minutes doing something active.
- Plan for your next tractor to include suitably low steps, handgrips, adequate doorway and cab space, and a safe mounting platform.
- Dismount by climbing down - not jumping down - and use each provided foot and handhold.
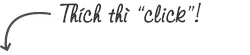